
#CAM SOFTWARE BLISK PROFESSIONAL#
From Delcam’s Birmingham headquarters, Professional Services offers CADCAM expertise and has access to machine tools in Delcam’s workshop that are used to verify and optimise the company’s CAM software. Nowadays, perhaps a third of the work carried out by Delcam Professional Services is customised work solving individual customers’ problems, says Mark Forth, Delcam advanced manufacturing product manager, taking in not only the cutting strategy but also the machine tool, fixturing, cutting tools, probing and inspection. Now the custom development operation of CADCAM developer Delcam, Delcam Professional Services, is working to drive down the cost of blisks by developing a new process by which to make them.
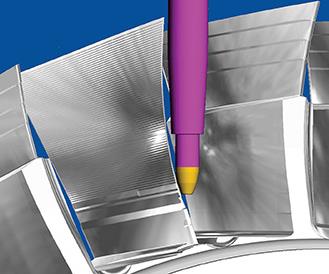
(In fact the Eurofighter and F-35 blisks are actually a hybrid technology in which blades are bonded to hubs using a special linear friction welding process). The Rolls Royce Trent XWB engine (intended for Airbus A350 commercial aircraft family), for example, is saving 15% in weight by employing blisks in some compressor stages: a savings that soon repays back the investment in reduced fuel consumption over the course of the engine’s working life.Īs they are machined from solid, blisks offer better structural integrity than discs, which consist of a single slotted hub into which are pressed separately made aerofoil blades.
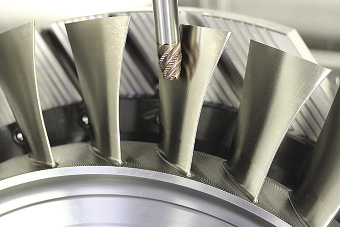
But there are signs that the blisk is moving into commercial aerospace. The word ‘blisk’ is a portmanteau of ‘bladed disk’: a solid ring of aerofoil blades ranged around a central hub these generate rotational motion from the force of air blowing through an aeroengine.īlisks have so far been found mainly on military aeroengines, for example in compressor stages of the EJ 200 Eurofighter engines and the vertical LiftFan for the F-35 Joint Strike Fighter.
